Peripherals: Tools and Devices for Efficient PLC Programming
PLCs are designed to run application programs – the programs controlling industrial equipment or processes – quickly and consistently. But how do you write, install and update such a program? That’s where programming terminals come in.
This article reviews the tools and devices used to program PLCs. It’s an area where technology has advanced rapidly in recent years, making programming easier and faster. The topics covered here are:
- Programming methods
- Input and output variability
- PLC peripherals
- Choosing the right tools for PLC programming
Programming Methods
One of the advantages of PLCs over PCs for industrial control is that they run only a single program. This means no other programs are competing for processor time, so the application can execute at a consistent and predictable speed.
However, a downside is that PLC CPUs don’t have any kind of integrated development environment (IDE) for writing and debugging programs. This is addressed in three ways:
- Programming terminals
- Programming by laptop
- Programming by handheld
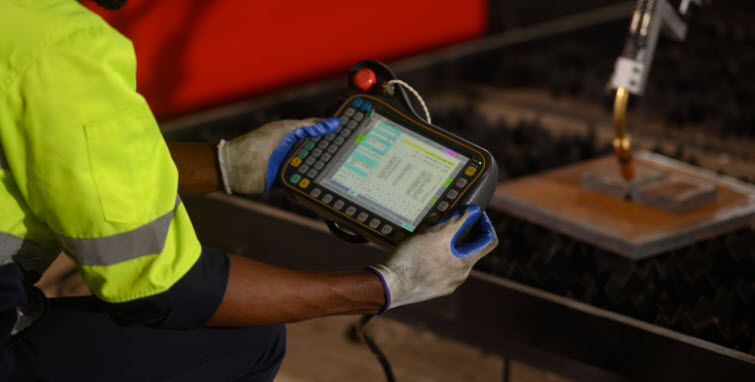
Programming terminals
This is a box that attaches to the PLC, often using a serial cable or sometimes a manufacturer’s proprietary interface. The box looks much like a calculator, with a keypad, a display, and often a number of specific function keys.
The PLC technician uses this terminal to access the application program on the PLC. Code is displayed on the screen and the technician can make edits, delete lines, and insert functions as needed.
PLC manufacturers developed their own proprietary terminals, so to connect to an Allen-Bradley PLC you needed an AB terminal, and so on. This means if you’re asked to work on an old PLC you may need to track down the appropriate terminal.
Today though, things are different. Rather than dedicated programming terminals, PLC manufacturers provide what we might call, “soft” terminals.
Programming by laptop
This is how almost every PLC is programmed today. The software is specific to the brand of PLC, so, for example, to work on AB PLCs the PLC technician will use the Rockwell Automation Studio 5000 development environment.
Laptop software lets the technician program in a variety of ways. There’s still ladder logic, but there’s also the option of using text or graphical programming methods, including function block diagrams and sequential flow charts.
The programming laptop is usually connected to the PLC over Ethernet, although USB is sometimes an option. An emerging trend is wireless connectivity, using Bluetooth or possibly Wi-Fi.
Programming by handheld
With wireless connectivity, it’s becoming possible to access the PLC code using an app on a cellphone or tablet. This has some limitations in terms of the ability to view and edit the program, but can be a useful tool for troubleshooting production process problems.
Input and Output Variability
When editing a PLC program, it’s important to remember that while the application program executes predictably, the same can’t be said of inputs and outputs. Analog signals in particular take time to rise and fall, and the programmer must allow time for inputs to be captured and outputs sent.
Digital signals can also have delays, resulting from how specific sensors function and how devices respond to output signals. Again though, the PLC technician must allow time for this, and should include checks to verify signal transmission and receipt.
PLC Peripherals
A PLC communicates with the outside world via a number of modules. These are:
- The HMI: This is the screen where the PLC shows what’s happening in the process it’s controlling. It may also allow an operator to set various values such as speed, distance or temperature. While some HMIs can allow access to the application program, it’s seldom practical to make changes over this interface.
- I/O modules: Enable the receipt and transmission of signals from connected sensors and devices.
- Communication protocol modules: Support USB, Ethernet, serial or other forms of communication. (May be needed to send process data to a SCADA system.)
Specialized functions: Motors are an example of devices where control may need a dedicated PLC module.
Choosing the Right Tools for PLC Programming
Most PLC technicians will find a laptop is their main programming tool. It’s portable, has a high resolution screen for viewing the application program, and can run software from multiple PLC manufacturers.
Some technicians still like to use programming terminals occasionally. They are more robust than a laptop, and may be needed to access programs on legacy PLCs. Their dedicated function keys can be faster than working on a laptop.
Handheld devices running apps from PLC manufacturers have their place. Few technicians will want to make them their sole programming device though.
Learn More
Programming a PLC is very different to writing a program to run on a PC. Historically, a PLC technician would use a programming terminal but today those have been replaced with PLC manufacturer’s software running on a laptop.
If you’d like to learn more about PLCs, their components, and how to maintain them, George Brown College can help. Call 1-888-553-5333 to speak with a Program Consultant.