What Are the Essential Elements of a PLC System?
The world of manufacturing has been changing rapidly over the past decade. Processes are largely automated and as a result, the quality of products that are produced and the efficiency of systems that produce them is at an unprecedented level. Despite these changes, programmable logic controllers have remained a critical component of these systems despite being invented in the 1960s.
PLCs come in a variety of sizes and with different capabilities, but all include the following six essential systems:
-
Central processing unit
-
Rack or mounting
-
Input assembly
-
Output assembly
-
Power supply
-
Programming unit
Here’s an overview of each and what they do.
Processor or Central Processing Unit (CPU)
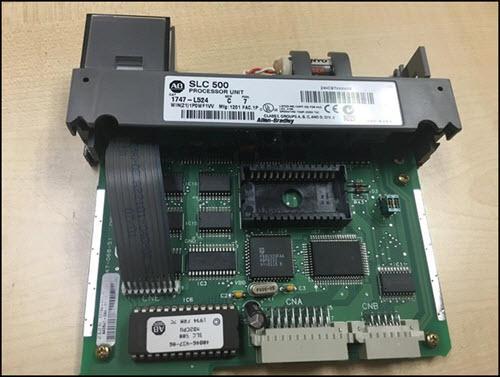
Often referred to as the “brains” of the PLC, the processor or central processing unit is responsible for the execution of commands. The industry has made an effort to use a standardized list of programming languages, namely:
-
Structured Text
-
Ladder Diagram
-
Sequential Function Chart
-
Instruction List
-
Function Block diagram
In spite of aforementioned list of languages being used, it’s important to note that each manufacturer has a different method of implementing the code.
Rack or Mounting
Though not a universal truth, most medium to large PLC systems are assembled so that their individual components (things like the CPU or processor, the I/O, and power supply) are held together within a mounting or rack. Smaller PLC systems often contain all of the components into one compact housing (often referred to as a shoebox, or brick).
Input Assembly
In terms of functions, the input assembly has two. The first is to receive external signals from field devices and control stations (switches, sensors). The second is to display the input point status.
Output Assembly
Outputs are the pieces of equipment used by the PLC to execute the commands, and are typically used to control a manufacturing process (motors, pumps, actuators, lights, etc.).
There are two types of I/O: Analog I/O and Specialty I/O. The differences between the two are outlined below.
-
Analog I/O refers to inputs and outputs that are responsible for a range (e.g. the running speed of a motor). This type of input operates based on continuous change of variable ranges (temperature, pressure, etc.) In this case, the output would include setting the speed of the motor.
-
As the name implies, Specialty I/O performs specific tasks, controlling things like high speed counters. Digital I/O operates in using a binary change (yes/no or on/off).
The PLC Technician program uses the PLCLogix simulation software to teach students about the I/O assembly. The image above is an example of the software’s interface, containing two discrete input modules, two discrete output modules, two TTL modules for BCD control and display, and two analog modules.
Power Supply
If the CPU is the brains of the PLC, then certainly the power supply is the digestive system, commonly supplying the unit with a 24VDC or 120VAC line voltage. The power supply status is continuously monitored and can include a switch for selecting a particular programming mode. Thanks to the power supply’s integral lithium battery, in the event of a power failure the contents stored in memory will not change from what they were prior to the loss of power.
Programming Unit, Device, or PC/Software
The modern PLC is programmed using a programmer or software that is built using a PC or laptop and then loaded into the PLC. PLC software’s big advantage is that they can run simulations to see how a PLC system will perform in a virtual environment. RSLogix is one of the most popular simulation tools today.
At George Brown College, our students learn using these same virtual environments. We use PLCLogix software, which emulates RSLogix and provides the ability to test and practice PLC programs. Students can apply the knowledge acquired from this program in the real world PLC environments.
PLCs Are More Relevant than Ever
In truth, it’s difficult to imagine a world in which PLCs did not exist. The manufacturing process would certainly not be what it is today, and would likely rely more heavily on greater quantities of human capital to achieve similar levels of production. Even though the base technology responsible for the typical PLC is decades old, PLCs remain a crucial component to manufacturing, robotic and automated systems.
Interested in learning more about PLCs? George Brown PLC Technician program offers you the foundation you need to get in on this exciting field filled with possibilities.