Proactive Maintenance Strategies for PLC I/O Modules
If the PLC is the brain behind industrial automation, the Input and Output module (or I/O module) is the central nervous system. Similar to maintaining a healthy nervous system within the body, manufacturers must ensure that the equipment used to execute the commands of the PLC and the transfer of data to and from the field is adequately maintained.
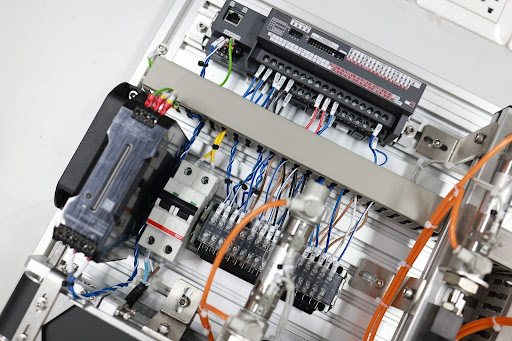
While it’s easy enough to wait for a piece of equipment, like the I/O module, to break down before executing a repair order, waiting until such a failure halts operations can be an incredibly costly strategy. For that reason, it is best to adopt a plan that allows you to perform routine inspections and identify and address potential problems before they arise. In this article, we’ll learn why it’s important to maintain your PLC and I/O module and how to do it.
What is the Benefit of Maintaining Your PLC?
Modern industrial automation is very much dependent on a properly functioning Programmable Logic Controller (PLC). A PLC is a rugged, industrial computer that uses custom programming to control and monitor the field devices operating on the factory floor. Because so much equipment is reliant on the PLC, it is integral that a stringent preventative maintenance schedule be followed to identify and address any component that may be at risk of malfunctioning. Since most factory equipment should receive regular scheduled maintenance, spending time to ensure the PLC is operating optimally adds very little in terms of overhead and yet, doing so can save a company a considerable amount of time and money.
What is an Input and Output Module?
The Input/Output module, or I/O module, is the part of the PLC that manages the transfer of information between the PLC and the control devices in the field. It is also responsible for controlling machine function and is particularly useful in systems that include older equipment that cannot otherwise “communicate” with the network. Core functionality of an I/O module includes:
Error Detection. Since I/O modules are vital to the data transfer process, they play a crucial role in the detection of errors within the system. This information is then sent to the CPU, which is then disseminated to an operator that can facilitate the resolution of the detected error. Error detection via the I/O module is often done using the “parity bit method”. In this method, an extra bit is added to a binary message that uses an odd or even number of 1’s. If during the transmission of the message, a 1 is changed to a 0 or a 0 to a 1, it effectively means that the odd or even count is different than expected, indicating that an error has occurred.
Processor Communications. The communication process itself includes a number of different functions, the first being command decoding wherein the I/O module receives and “decodes” the commands that are sent to it from the processor. The second function is the exchange of data, wherein the I/O module facilitates the transfer of data between the processors and field devices. Lastly, there’s address decoding. This function requires the I/O module to manage the unique addresses of each device connected to it.
Data Buffering. Data buffering allows the I/O module to control the speed of the data sent between the processor and the field devices. In doing so, the I/O module compensates for the latency experienced by the field devices.
Control and Timing. The I/O is specifically designed to manage the transactions that occur between the system and the field devices.
How to Properly Maintain an I/O Module?
As with any other piece of industrial equipment, the best way to ensure the I/O operates optimally for as long as possible is to employ a comprehensive maintenance strategy. The strategy of implementing a routine check of the equipment paired with regular data backups and firmware updates will greatly improve the likelihood that the I/O module will continue functioning as intended, perhaps even beyond its life expectancy. With that in mind, here are a few tasks that you can perform during the preventative maintenance of your I/O module.
Visually inspect and clean the I/O module on a regular basis, even going as far as adding this task to a daily or weekly walkthrough of the facility. This includes the removal of dust and inspecting the module for signs of wear and tear.
Check the module’s connection to the power supply. Visually inspect and tighten any electrical connections that may have come loose since the last inspection.
Perform diagnostic tests. Running a diagnostic test of the I/O is a reliable method for identifying inputs or outputs that are not functioning to spec. Replace any faulty I/O in a timely manner.
Don’t ignore the error logs. PLCs can be configured to provide users with detailed error logs. This resource will often provide insight into a potential component failure.
Reactive Maintenance is Never the Right Choice
Hindsight may be 20/20, but having the foresight to develop a proactive maintenance plan, particularly where crucial infrastructure like the PLC and I/O module are concerned is much more valuable. In an information age, it seems implausible that some operations still haven't found the value in following a maintenance strategy that emphasizes timely repairs and replacements while mitigating downtime. If you would like to learn more about PLCs, their components, and how to maintain them, speak to a program consultant at George Brown College today by calling 1-888-553-5333.
Comments
Thank you for your inquiry!
Submitted by hazna on Tue, 10/29/2024 - 11:52
Hi Dylan,
Thank you for your inquiry regarding the online PLC Technician Certificate program from George Brown College.
To know more about our programs, you can speak to one of our Program Consultants toll-free at 1-888-553-5333. Or if you would like to register for our programs, you can do so online at https://www.plctechnician.com/how-to-register using a credit card or by calling us at the above toll-free number.
Thanks
Importance of Proactive Maintenance for PLC I/O Modules
Submitted by Devanshu (not verified) on Sat, 11/30/2024 - 01:54
Great post! Proactive maintenance for PLC I/O modules is crucial for preventing costly breakdowns and ensuring smooth operations. Regular inspections, data backups, and diagnostic tests help extend the life of these vital components. I especially liked the emphasis on error detection and the importance of staying ahead of potential issues rather than waiting for a failure.
I'm an industrial maintenance engineer and I need more plc skills